
ZERO-water
process pipe
heating
Adding ZERO-water to ZERO-carbon
CATTS Sustainability
in its true
form
-
IETF funding
-
Super Tax deductions
-
Major brand funding available
89%
Energy reduction compared to traditional water systems
0
Zero carbon ready
0
Zero water
0
Zero contamination risk
CATTS
WATER FREE
PROCESS PIPE HEATING
-
Up to 89% energy saving.
​
-
Removal of hot water from your process - no contamination risk.
-
Remove gas as a fuel, no spiralling gas prices for the future.
-
Reduce your chiller load, saving even more operational costs.
​
-
Thermodynamic core keeps hot spots away - no burns or scorching.​
-
Intelligent control system with advanced cascade built-in.
-
Virtually maintenance free - no mechanical moving parts.
​
-
Digitised system with factory NET compatibility.
​
-
Automate with your plant - auto change setpoints; you can even create your own thermal profile..
CASCADE AND THERMODYNAMIC TRANSPORTATION SYSTEM
CATTS
A revolutionary new energy saving process heating system that can be fitted to new process pipework or retrofitted to traditional, dual-walled, water-jacketed pipework.


Saving Energy by up to 89%
​
CATTS is big news. As verified by Sheffield Hallam University's National Centre of Excellence for Food Engineering, it allows users to save up to 89% of energy usage compared to traditional hot water heating systems, and that's big, especially across a whole factory.
No longer heat your chocolate rooms to 40°C as a
by-product - heat what is required and where it is required - in the process.
​
Removing Water from your Process Heating

Traditional water jacketed design, a water jacket around an inner pipe
​
Chemically treated hot water for pipe and equipment heating, together with foodstuffs, don't make for a good mix, especially when they do mix!
​
And unfortunately, mix they do, when you least want it. Traditional pipe heating using water is lined up to fail. Corrosion will start to take hold of the inner product pipe, forming micro-pit holes that eventually break through into the product.
​
That does take a while to start to happen, but then you have those unexpected leaks from joints and fittings that usually end up where you dont want them to be.
​
The risk of microbe or chemical contamination using traditional hot water methods is eliminated when using CATTS.
​
​


CATTS
CHILLER LOAD REDUCTION
- A BETTER PRODUCTION AREA
If you have a water process pipe heating system, you will already know
how most of the heating energy ends up in the room. Just heating the process, and not the room, will have very desirable side effects:
-
Be able to turn down your chiller air conditioning system, dramatically saving you even more energy.
-
Experience more uniform room temperatures throughout the seasons, reducing manufacturing problems due to excessive environmental temperatures.
CATTS
INSTALLATION

CATTS can be installed on new process pipe or retro-fitted to existing water jacketed pipe (in the latter, we remove the water and plug the stub-in).
Depending upon the pipe size, we will tailor make a system to your specifications.
A typical power installation will depend on the pipe size and if you require a melt-out facility.
Running power will be extremely small, proven (and verified by Sheffield Hallam University's National Centre of Excellence for Food Engineering)
to be approximately 12 Watts per metre on a 2" pipe, insulated and running with chocolate.
With a melt-out option, ZECK aim to install approximately 60W/metre, giving you a total run length of approximately 60m on one 16A feed.
CABLE CONTAINMENT
What's probably not obvious so far is that this system has been designed to carry all power, communication and signal cables internally.
As experienced engineers in factory installations, ZECK know how expensive containment can be for a factory environment. Stainless traywork, basket, ladder racking, and dairy pipe can bump the cost up massively on electrical installations.
That's why ZECK provide completed spool sections (up to 3m) with all the necessary cabling built-in to the CATTS housing.
Most systems will be able to run this way for up to 60 metres. As a customer, you only need to provide a 16A single phase supply plus a PROFINET connection to the first spool at each 60m point, and we look after the rest.
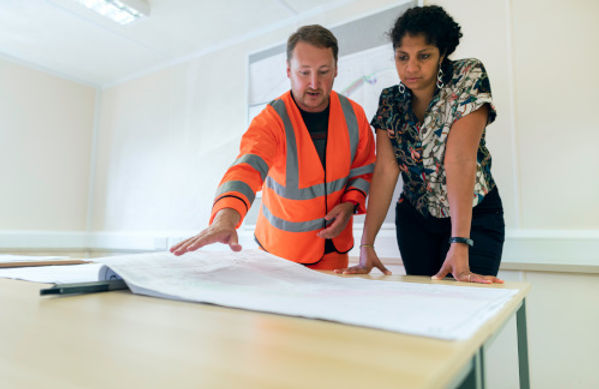

PRE-TESTED - Plug & Play
ZECK build the whole assembly off-site, including the pipe spool, with heating system, microcontroller, PROFINET cabling, power feeds and sensor systems as a completed spool unit.
Before shipping to site, each item is thoroughly tested, so that when it arrives it is a simple matter of connecting the spools together mechanically and then plugging together the electrical systems.
This speeds up installation dramatically on-site.
As a customer you will have minimal down-time and a system that will be up and running quickly, with the confidence that everything has been pre-tested off-site.
CATTS
CONTROL
There are two main parts of the CATTS system that make this such a powerfully clever design.
The first is the Thermodynamic Core, explained above, which transmits heat at 30 m.p.h. down the entire length of the spool and gives an iso-static thermal profile (even throughout).

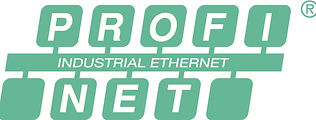
ZECK is a registered PROFINET manufacturer, ID 1513
The second most important part of the system is undoubtedly the control side. ZECK use their tried and tested Cascaded PID Control system, as proven to be extremely successful in a lot of the ZECK product range.
Unique to CATTS though, is a powerful Siemens based microprocessor system, designed bespoke for ZECK by ESYSE, a major controls supplier to Siemens themselves.
ESYSE designed a powerful microprocessor system which can handle PROFINET communications together with cascaded PID control. This brings the digital interface right to the end-user's PLC.
DIGITISE YOUR PLANT
As keeping a product warm and flowing is critical to a manufacturing plant, ZECK understood the need for the system to keep running successfully even when the network might be down.
Chopping through a network cable or perhaps leaving one unplugged, are some of life's unfortunate events. But the ZECK controller on the CATTS system does not need the network to be available to operate successfully. All ZECK controllers operate to the last command, and keep operating, even with loss of signal.
CONTROL REDUNDANCY
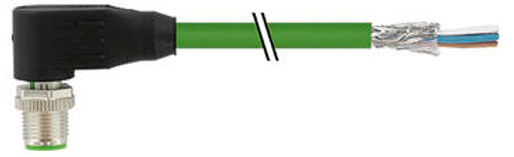

Each control loop uses dual sensor technology in the cascade loop. The first sensor monitors the actual heat source deep inside the CATTS spool assembly. Instead of allowing the heat source to free-run until the process is at temperature, the CATTS controller modulates the heat source and holds it back to the right level when the process is still demanding heat. This is a key fundamental to managing the correct amount of heat flow into the sensitive product. This internal sensor is continually auto-calibrated (every second) using ZECK's clever know-how, against the product sensor.
The second sensor, the product sensor, is in contact with the wall of the pipe and this sensor is manually calibrated. It is housed inside the control Pod on the pipe spool and is easily removable in a few minutes for testing or replacement.
SENSOR CALIBRATION
CATTS
INTERFACE

In collaboration with Meson Electrical Services, ZECK explained the requirements for the PROFINET communications system and they designed the PROFINET interface on the Siemens S7 PLC and with it a set of user interface screens.
Shown to the left, an Engineer's setup screen displaying a password protected area for adjusting the cascade and the PID system.
But don't worry, as a customer, ZECK will be on-site to commission and set up the system. Once set up, it will be a matter of leaving it to run 24/7.
With PROFINET enabled CATTS systems, the world is your oyster. Link the system to your factory NET and you can interrogate every pipe spool, look at trends, spot potential issues, set multiple temperature setpoints automatically with different products in the pipe - in essence, unlimited control.
CATTS
MAINTENANCE FREE - VIRTUALLY
​
All CATTS systems use solid state switching with heating cores that are extremely robust and proven for decades.
​
No pumps, chemical dosing, bearing wear, leak fixing, pressure valves, header tanks, blown gaskets, pressure stalls, rattling feed pipes. No footprint space for calorifiers and water pipe runs. What's your maintenance fitter going to be doing now? More cost savings ahead.
​
All we ask is that you have a general check up once a year, which takes a day's site visit on most systems.
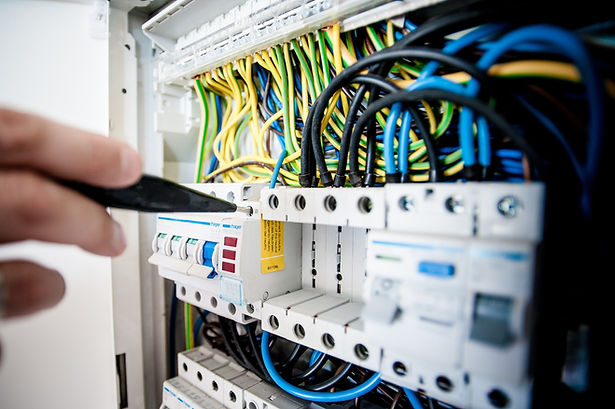
THE CATTS CORE
RELATED NEWS/PROJECTS

RELATED PRODUCTS
KEY FEATURES THAT COULD BENEFIT YOUR BUSINESS
Energy Savings

ZECK systems are up to 89% more efficient than old technologies

Digital Control
Switch from analogue to digitally controlled precision

Dry & Hygenic
ZECK's electrical process is dry, hygenic and non-corrosive heat